Steel mill ladles have limited lives. As their refractory linings wear or develop breaks due to shock, the outer part of a ladle can be exposed to excessive temperatures. If not caught in time, the result can be ladle disintegration and a molten metal breakout, threatening the lives of workers and destroying equipment. FLIR thermal imaging camera systems are used to monitor ladles in real-time and warn of a breakout before it happens, saving hundreds of thousands of dollars by preventing injuries, equipment damage, and production downtime.
Ladle Safety
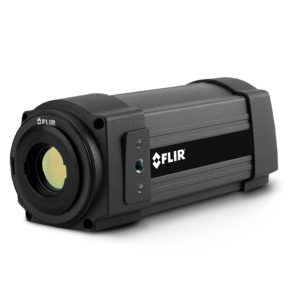
It is well known that refractory linings in steel mill ladles have limited lives, and useful life may be shortened even more due to the breakage of refractory bricks from mechanical shock. As the lining wears or develops breaks, the outer part of a transport ladle can be exposed to molten metal. If not caught in time, the result can be ladle disintegration and a molten metal breakout, threatening the lives of workers and destroying equipment.
Fortunately, thermal imaging cameras can detect hot spots on the ladle that warn of a failure far sooner than a visual inspection. This allows the ladle to be taken out of service in a timely manner and scheduled for relining exactly at the right time and at the optimum replacement cost.
Ladle Monitoring System
Usually, the thermal imaging camera from FLIR is placed in robust housings and located in fixed positions where they have a clear view of a filled ladle as it passes by on the gantry crane. Those cameras capture video images of the ladle in real-time and calculate temperatures over the ladle’s surface. A few cameras can cover the entire surface of the ladle, but typically a few regions of interest (ROIs) are predefined for closer scrutiny and analysis. The thermal images of ROIs where failures are more likely to occur can be stored in PC memory for later comparison to current images. Defining ROIs also allows FLIR’S IR Monitor software to ignore high temperatures on objects around the ladle that are within the camera’s field of view (FOV), which in turn lowers the number of unwanted alarms.
These thermal video images and corresponding temperature data are carried over Ethernet and fiber optic cables to the industrial PC, which avoids problems from the electrically noisy mill environment.
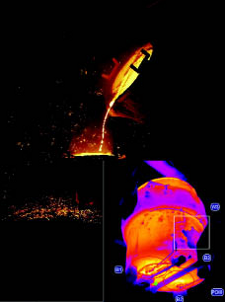
The IR Monitor software can then compare each image frame from a camera to the image templates stored in PC memory. This gantry crane operator does not have to stop the crane at any particular location to capture images and the production can continue smoothly. When there is a match between the template and the corresponding portion of a camera’s FOV (i.e. one or the ROIs), temperatures are calculated. If the temperature exceeds the ladle’s predefined parameters, an alarm is triggered. The exact parameter temperatures for alarms can be adjusted easily, based on mill experience.
The ladle monitoring system will automatically recognize predefined regions of interest (ROIs) and compare the measured temperature with previously set parameters.
Alarmingly high temperatures
The alarm could be just a warning if the temperature isn’t too high, and movement of the ladle to the converter mill can continue. The operator can then compare the warning temperature to a trend analysis done by the software to determine if the ladle can remain in service for another pour.
If the ladle temperature is above a critical level, however, an emergency alarm will be triggered which will immediately stop the gantry crane movement. Also, alarm messages and images can be sent to a mill manager’s office via Ethernet, email, or FTP.
Typical Setup
The schematic illustration on this page depicts a typical setup for an automated Mill Ladle Refractory Monitoring System using the FLIR Camera. Although the analog video and digital I/O outputs from this camera allow it to operate as a standalone smart sensor, most steel mill applications use its digital data stream, sent over Ethernet lines, in computer-controlled automation systems. The camera’s Ethernet interface can supply the camera’s video signal to virtually anywhere and facilitates monitoring from multiple locations.
FLIR’s IR Monitor software is used to control all camera functions, collect temperature data, display thermal images, and perform data analysis. The operator’s display is the primary interface for alarm functions.